Imperial Electronic Assembly, Inc.
We have been extremely pleased with the implementation of Inovaxe’s InoAuto Smart cart units into our operation at Imperial Electronic Assembly, Inc. located in Brookfield, Connecticut. We are an EMS provider that understands in an ever-competitive environment, electronic manufacturers and assemblers must be highly efficient in responding to rapid business and technological changes. Frequent plan modifications, shorter product life cycles, and increased product complexities are all part of the daily challenge. We strive to manufacture a high-quality product with a flexible schedule to satisfy all of our customer demands while still minimizing the cost of operations. This made choosing Inovaxe’s ultra-lean Smart storage solution an easy decision for us.
Our supermarket of Smart carts is located on our production floor adjacent to our Panasonic SMT lines, eliminating the need to store parts in a separate stockroom location. Our supermarket contains six full-size InoAuto Smart cart units for storage of 7 and 13 inch reels of various tray widths. Based off the widths of active reels in our inventory, Inovaxe was able to determine the best configuration for our carts and designed our system to store more than 3,700 reels in a mere 28.13 square feet of floor space.
The ability to fully integrate the InoAuto software with our PanaCim software was key in our decision making process and has become crucial to our procedure. It provides us with real time data transfer between the equipment and the ability to track reel quantities to minimize the amount of open packages per part number. This functionality has increased our inventory accuracy and helped to avoid line down situations.
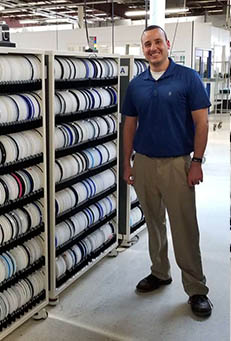
With the implementation of the Smart carts, we have virtually eliminated the kitting process. We now have the ability for our SMT operators to call the next job from PanaCIM and watch as the required reels light up in the Smart carts. The carts then prompt the operators to pick the reels in feeder location order allowing them to load the reels onto the feeders right as they are pulled from the carts. If any reels are pulled out of sequence or the wrong reel is pulled, an error message will occur and stop the pick process to ensure we are getting the correct reel every time. There is no more sorting through disorganized bins to find the correct reel and multiple operations have been reduced to one quick process!
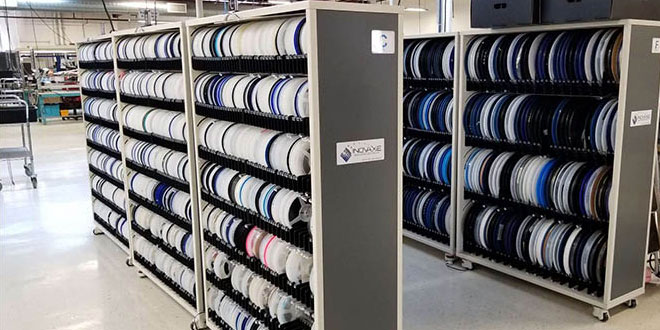
Not only has the kitting process improved, but returning reels to stock for storage has never been easier. After completion of a job, we no longer have to worry that a reel may potentially be placed in the wrong stock bin back in the stock room. We simply have to bring the reels back to our Smart carts, scan the reel and place it in the closest available location. The carts store this information and will send us right back to that location the next time the reel is needed. Nothing gets misplaced and we no longer spend hours of downtime sorting through boxes of reels to find a misplaced reel needed for production.
The benefits of implementing the Smart carts have been realized throughout our entire organization. Some of our key improvements since implementation include:
- Obsoleting our third SMT line, an older line that is not compatible with the PanaCIM software. After shutting down this line we have still seen an increase of 10-15% in throughputs due to the efficiencies gained from our new processes.
- Reducing SMT material handlers from 4 to 1 allowing us to transition these 3 positons into other processes in our operation.
- A substantial reduction in set-up and downtime leading to a more steady and efficient work flow. One of our most complex and steady runners used to take roughly five and a half hours to kit and an additional hour and a half to set-up. We have now reduced this entire process to 45 minutes. The efficiency is tremendous!
Working with the Inovaxe team during the installation and integration process with Panasonic couldn’t have gone any smoother. The team is professional, informed, and has the flexibility to always be available to support our needs. We could not be more pleased with Inovaxe’s ultra-lean Smart material handling system due and its ability to solve our material handling and storage challenges. I would not hesitate to recommend Inovaxe’s Smart Material Handling Solutions!
Tony Conte / President
Imperial Electronic Assembly, Inc.
Omron Automotive Electronics, Inc
We are very satisfied with the Inovaxe Smart Cart as it helps operators replenish feeders efficiently as well as add valuable space on the floor. The size of the cart is compact and mobile at less than 5 feet. The Smart Cart stores hundreds of reels ranging from 7” to 15” and comes in a variety of widths, which helps operators identify the parts required for the kit in seconds. Before, we manually stored and replenished reels which would lead to possible errors and extended operator time searching for parts! By using the Smart Cart everything is in the system and saves so much time for us. The Smart Cart has been very dependable, as it is battery operated and lasts several hours.
The Inovaxe team including John, Mike and David always assists with troubleshooting any problems and resolving issues quickly. Whenever we have questions they always know the answer and provide wonderful customer service. The Smart cart is a valuable tool for the SMT production floor as it quickly identifys reels and reduces costly operator errors. I highly recommend the Smart Cart to any company! Below are pictures of the old carts we utilized and the drastic difference this Inovaxe Smart Cart makes.
Tippy Wicker / Mfg. Operations Manager
Omron Automotive Electronics, Inc
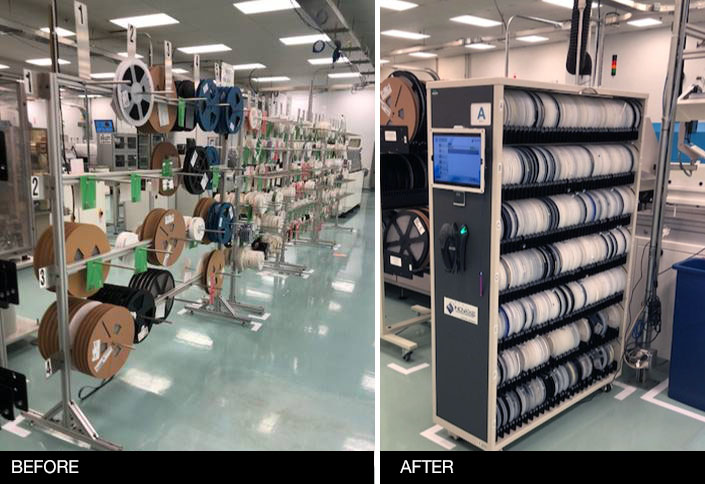
Partial Client List
Siemens Manufacturing Co. Inc.
We purchased the smart cart about 2 years ago. Since inception we have not lost a reel of parts. In the beginning we were not putting used reels back on the smart cart correctly. It flashes red if you put a part in without scanning. The smart cart also has an audit feature that will let you know if a part is missing or an extra part where there shouldn’t be one. When we do our audit now we don’t usually find any errors. The smart cart is working great for us.
Mark Voss
Production Manager
Siemens Manufacturing Co. Inc.
Javad EMS Inc.
Since incorporating the Inovaxe InoAuto Smart material handling system into our operation here at Javad EMS, we have received all of the benefits promised to our operation and more. We have not only reduced our WIP reel storage space by approximately 70% but have done so while achieving finite location stocking over this inventory. We’ve reduced our material handling and feeder set-up time by greater than 50% with an expectation that over time to meet our 70% target improvement from before we had these carts.
We are a high mix, low to medium volume EMS provider and as such, quick and accurate product to product changeover is an integral part of our operation so it is critical for our manufacturing personnel to be able to quickly locate the parts that they are looking for! Our feeder set-up personnel pull directly from the carts eliminating the old process of kitting to them from our vertical carousels.
They’ve truly been able to conquer one of our largest challenges by lighting up the exact location of the reel we need! Likewise, once a job is complete and off our SM machines the smart technology of the carts allows for the de-kitting process to be much smoother and easier as we have eliminated the extra steps and transactions necessary to place a part back into storage.
The Inovaxe team is made up of true professionals that are always available to take on our custom requirements and exceed our expectations.
Gary Walker / Vice President
Javad EMS Inc.
DRS Technologies, Inc.
Inovaxe Point of light systems are one of the best investments DRS has made as far as inventory control goes. We were averaging 7.5 hours a day looking for parts in kits throughout the production floor by more than 1 associate. With us bringing in the Point of light system we have cut that time down to 45 minutes. The reason for the dramatic change was that we were able to load our point of light cart with 2 months’ worth of parts and call them up when we are running kits.
The point of light system has saved us on average 35 hours a week of wasted time looking for parts in kits throughout the production floor. For any company that spends a large amount of time tracking parts for production use the Inovaxe Point of Light system is a great answer because not only organize where parts are stored it also allows companies to keep an accurate inventory count of the parts in the system. The extra bonus of the system is that it is very easy to use and does not take long to train new associates in the proper use of the system. DRS has bought 2 systems with a 3 in review.
William Capen / Senior Mfg Engineer
DRS Technologies, Inc.
VTC (Veterans Trading Company)
The Veterans Trading Company (VTC) Team has been using the Inovaxe Smart Cart system since the grand opening of our newest facility in 2018. We started out with three of the Carts and have expanded to six over the course of three years as well as adding lots of additional shelf locations for tracking our various product types.
Working with the Inovaxe team has greatly helped in make our system work more efficiently and accurately. If for some reason we have a problem come up they are always friendly and helpful in getting us back on our feet. Their team is also very knowledgeable when talking about different solutions and what may be the best solution for our specific needs.
Charles Mahoney / SLC SMI Business Process Analyst
VTC (Veterans Trading Company)
Surf-Tech Manufacturing Corporation
We began looking at Inovaxe in 2020 and decided to purchase in 2021. The main purpose was to electronically keep track of where our SMT reels were. We chose them because they are the industry leader and they work very closely with Hanwha. Since we already use the Hanwha inventory tracking, partnering with Inovaxe made good business sense.
Initially, we had to work with Inovaxe to help fully integrate our system with Hanwha’s database and our ERP software. The technicians were very helpful in getting this set up. The installation is a DIY, and we had no issues getting it unloaded or placed on our floor.
Stephen Eggert / President
Surf-Tech Manufacturing Corporation