Solutions for SMT Material Handling and Accuracy Issues
Inovaxe News
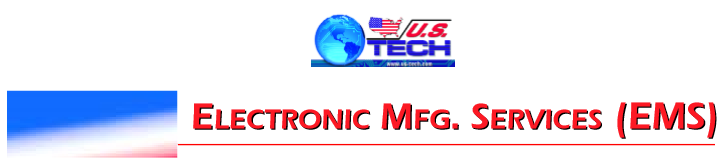
Inovaxe’s Smart Storage Technology Helps Imperial Electronic Assembly Stay Lean
By Margy Khoshnood, Vice President of Sales, Inovaxe Corporation
Download the article as a PDF here.
Headquartered in Brookfield, Connecticut, Imperial Electronic Assembly, Inc., is a privately owned contract electronics manufacturing services company offering world-class assembly and test capabilities. Its expertise ranges from printed circuit board assembly (surface mount and throughhole) to any aspect of cable and harness manufacture to completed electromechanical rack and black box assemblies.
Imperial takes pride in its quality service and operates in a quality system registered to AS9100C:2009 and ISO 9001:2008. Each employee participates in an extensive training program that includes IPC-610 and J-STD soldering standards and ESD control. Imperial handles engineering changes in a professional and timely manner, and routinely offers suggestions for product improvements. Additionally, the company has UL certification and is an AMP ACES account.
Established in 1988, the company has enjoyed sustained, healthy growth. In 2001, it expanded operations by acquiring a 45,000 ft2 (4,180.6m2 ) facility that has become the home of Imperial’s state-of-the-art equipment and highly trained staff.
Imperial is a company that values quality and innovation. Finding a storage solutions partner demonstrating similar qualities was a necessity and it became apparent early in the research process that Inovaxe was a company whose values aligned perfectly with Imperial’s.
Smart Storage Carts
The company purchased six fullsize Inovaxe InoAuto Smart cart units for storage of 7 and 13 in. (17.8 and 33 cm) reels of various tray widths. Conte refers to the machines as a “supermarket” located on the production floor adjacent to his Panasonic SMT lines, eliminating the need to store parts in a separate stockroom location.
Based on the widths of active reels in the company’s inventory, Inovaxe determined the best configuration for Imperial’s carts and custom designed a system to store more than 3,700 reels in a mere 28.13 ft2 (2.61m2)of floor space.
Conte noted the ability to fully integrate the InoAuto software with Imperial’s current PanaCim software as a key part in the decision-making process and has become crucial to the company’s procedure.
“It provides us with real-time data transfer between the equipment and the ability to track reel quantities to minimize the amounts of open packages per part number,” says Conte. This functionality increases the company’s inventory accuracy and avoids line-down situations.
The SMART InoAuto ultra-lean material handling systems enable users to locate parts in less than four seconds and return a part in less than eight seconds. The carts are mobile or fixed, store from 560 reels in 2.5 ft2 (0.23m2 ) or store 1,120 reels in 4.5 ft2 (0.42m2 ), with a return on investment of less than six months.
Inovaxe has provided manufacturers with the capabilities to substantially streamline their material handling systems and achieve a wide range of benefits, including: more than 90 percent labor reduction in pulling kits and returning parts; more than 90 percent space reduction for storing SMT parts and kits; reduction of set up time and increase in machine uptime; reduction of operator travel time by 60 percent; elimination of paper for kit pull and feeder loading operation; traceability to each of the smart transactions; drastic enhancement of inventory accuracy, without counting parts; and a substantial reduction of errors in feeder set up.
Improved Kitting
With the implementation of the smart carts, Imperial has virtually eliminated the kitting process. The SMT operators now have the ability to call the next job from PanaCIM and watch as the required reels light up in the smart carts. The carts then prompt the operators to pick the reels in feeder location order, allowing them to load the reels onto the feeders as they are pulled from the carts. If any reels are pulled out of sequence or the wrong reel is pulled, an error message will occur and stop the pick process to ensure that the correct reel is retrieved every time. There is no more sorting through disorganized bins to find the correct reel, and multiple operations have been reduced to one quick process.
Not only has the kitting process improved but Conte said that returning reels to stock for storage has never been easier. “After completion of a job, we no longer have to worry that a reel may potentially be placed in the wrong stock bin back in the stock room,” he says. “We simply have to bring the reels back to our smart carts, scan the reel and place it in the closest available location. The carts store this information and will send us right back to that location the next time the reel is needed. Nothing gets misplaced and we no longer spend hours of downtime sorting through boxes of reels to find a misplaced reel needed for production.”
The benefits of implementing the Smart carts have been realized throughout Imperial’s entire organization. Some of the key improvements since implementation include:
- Obsoleting the company’s third SMT line, an older line that is not compatible with the PanaCIM software. Even after shutting down this line, the company has seen an increase of around 15 percent in throughput due to the efficiencies gained from its new processes.
- Reducing SMT material handlers from four to one, which has allowed Imperial to transition three positions into other processes in its operation.
- Significantly reducing set-up and downtime, leading to a more steady and efficient work flow. One of its most complex and steady runners used to take approximately five and a half hours to kit and an additional hour and a half to set up. Conte says that the entire process has now been reduced to 45 minutes, resulting in extreme efficiency.
As for installation and customer service, Conte said that working with the Inovaxe team during the installation and integration process with Panasonic couldn’t have gone any smoother. “The team is professional, informed, and has the flexibility to always be available to support our needs,” he said. “We could not be more pleased with Inovaxe’s ultra-lean smart material handling system and its ability to solve our material handling and storage challenges. I would not hesitate to recommend Inovaxe’s smart material handling solutions.”
Contact: Inovaxe Corp.
260 SW 12th Avenue
Deerfield Beach, FL 33442
954-531-1363
E-mail: info@inovaxe.com
Web: www.inovaxe.com
Imperial Electronic Assembly, Inc.
1000 Federal Road
Brookfield, CT 06804
203-740-8425
E-mail: tony@impea.com
Web: www.impea.com
###
About Inovaxe Corp.
Inovaxe Corporation is focused on delivering innovative production and inventory management solutions to the electronics industry. The Company’s product offering includes ambient air Smart and Passive (InoAuto, InoCarts and InoKits) and Moisture Sensitive Device Material Storage Hardware (InoCart MSD), a Supply Chain Management System (InoVision), an inventory/kitting software management tool (InoView), and InoAuto Locator software for locating components. For more information and a demonstration of Inovaxe products, visit www.inovaxe.com